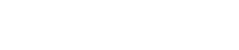
Conversion processes
The fundamental issue facing the modern refiner is that the market product mix is structurally lighter than the available feedstock (crude oil). In chemistry terms this means that many of the molecules found in crude oil are too large and that their average hydrogen to carbon ratio is too low. Refineries must therefore reduce the size of molecules by “cracking” but also increase that ratio. This can be done by either removing carbon or adding hydrogen. The most common conversion processes are Catalytic cracking, Hydrocracking, Visbreaking and Coking.
Octane enhancement processes
Gasoline accounts for a large fraction of market demand for petroleum products. One of its key properties is the octane rating which determines its suitability for use in an internal combustion engine. Driven by engine efficiency, the required octane has increased over the years and processes have been developed to both enhance the octane rating of suitable fractions and produce more high-octane components.
Blending
All these refining processes produce a large number of product streams that are, as a rule, still unsuitable individually as marketable products. The fourth crucial stage of refining is therefore blending i.e. preparation of finished products from this variety of blending components. It is a complex balancing act between product quality, off-take commitments, loading capacities, process plants rundowns and storage capacity. This activity, managed jointly with crude and feedstocks supply, has received increasing attention in recent years, especially in a context of more severe and multifaceted product quality requirements.
Ancillary processes and utilities
A number of ancillary processes are required to support the main plants. These include:
Gas processing to clean and separate light gases, producing marketable LPG and fuel gas for the refinery. This includes removal of hydrogen sulphide for which an amine solution is normally used.
Sulphur recovery where the hydrogen sulphide recovered from the regenerated amine solution is turned into elemental sulphur.
Effluent water treatment whereby process water and surface runoff water are purified before being either recycled or discharged.
Although process heat is commonly supplied directly by fired heaters, refineries make wide use of steam that is produced in boilers. Many refineries also produce all or part of the electricity they consume. Many refineries have installed so-called Combined Heat and Power plants that efficiently co-produce electricity and steam. In most such cases, electricity production exceeds the refinery needs and the surplus is exported.
All modern refineries need hydrogen for hydrotreating, normally supplied by the catalytic reformer. Where hydroconversion processes are installed, however, additional hydrogen is required and is manufactured in a separate plant, usually by steam reforming of methane (natural gas).

SIMPLE REFINERY
A “simple” refinery typically includes crude distiller, catalytic reformer and hydrotreaters. An increasing number of refineries also have an isomerisation unit to enhance the octane rating of light naphthas. Several simple refineries have bitumen manufacturing facilities involving vacuum distillation and possibly bitumen blowing.
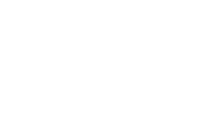

COMPLEX REFINERY
Today the structure of the market demand is such that complex refineries are required to supply the desired volumes of clean light products. As a result, the majority of EU refineries are complex. There is, however, a wide range of complexity from a relatively straightforward FCC + Visbreaker configuration to a fully complex site including FCC, hydrocracking, residue conversion and bitumen manufacture.
The majority of refineries worldwide, including the EU, have an FCC. This is often accompanied by an alkylation unit to increase yield and quality of the gasoline pool. In North America where heavy fuel oil markets are limited, most refineries have a coker. This is much less the case in the EU where visbreakers are usually installed.
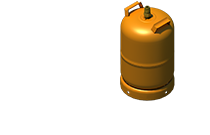
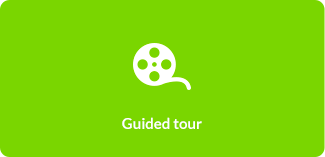
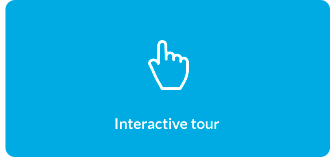

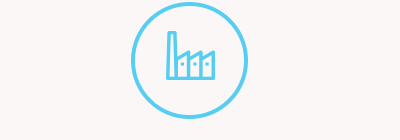
Energy markets worldwide are dominated by hydrocarbons the main source of which, along with natural gas, is crude oil. Whereas the former can be used as such or with minimum treatment, the latter is unsuitable for most practical applications. The purpose of an oil refinery is therefore to turn crude oil into products that are fit for end-use, in the quantities that are required by the market.
Over the years, markets have demanded increasingly sophisticated products as well as increasing volumes of lighter fractions, most notably transport fuels, while markets for heavier oils were decreasing. Refineries have had to continuously adapt to these changes, becoming increasingly complex in the process.
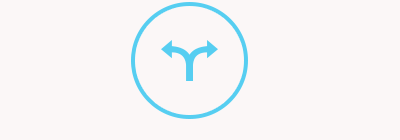
Physical separation according to boiling range (distillation) applies primarily to crude oil, although is also used at various stages of the refining process to fractionate the raw products of treating and conversion processes. Distillation towers of all sizes are a ubiquitous sight in a refinery.
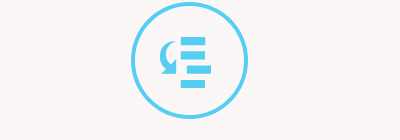
Treatment covers a wide range of processes designed to improve the quality of the products.

Conversion involves changing the nature and/or the size of the molecules to increase the yield of certain products.
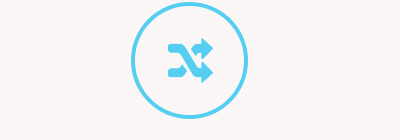
Blending is the final and crucial step where intermediate streams are used to produce finished products that meet all specifications.

All refinery products are produced simultaneously and, at least over a reasonable period of time, all products must be disposed of. Although refiners have some flexibility to change relative yields by varying operating conditions and using different crude oils, this is limited by a number of practical constraints. A refinery cannot just produce a single product!
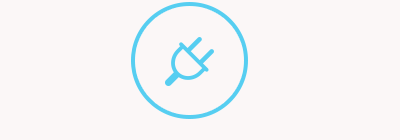
All refinery processes require energy. Refineries can in principle be self-sufficient and use a portion of their hydrocarbon intake as fuel. Although all refineries do this to an extent, many refineries import natural gas and/or electricity for either environmental or economic reasons.
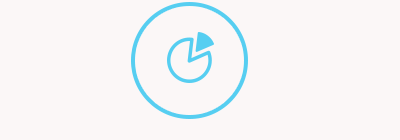
Energy represents a large proportion of refinery operating costs as a result of which maximising efficiency has always been a major preoccupation for refiners. This is in great part achieved through heat integration between heat producing and heat absorbing steps, making processes and indeed products highly interdependent.
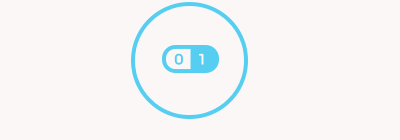
Refineries are often referred to as “simple” if they do not include conversion processes and “complex” if they do. This is somewhat arbitrary as, in reality, there is a continuum from the very simple to the most complex refinery. As examples we have illustrated a simple and a very complex refinery.
MAIN REFINERY OPERATIONS
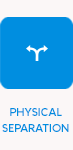
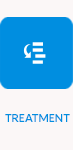

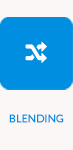
REFINING AT WORK
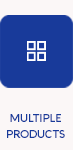
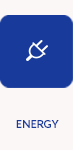
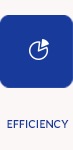
